Discover your training possibilities
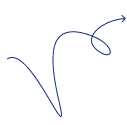
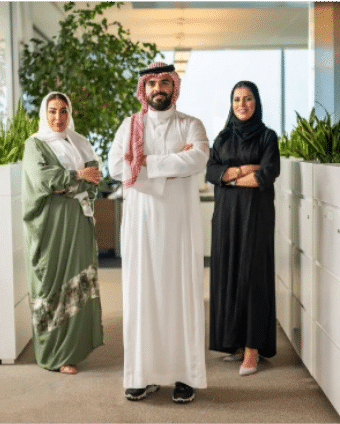
Design an approved training material
We are designing integrated training materials for better x5 training courses according to the standards of the General Organization for Vocational Training and the IMAS standards.
Interactive training materials
Training materials for online training in e-learning platforms (LMS), (SCROM)
We are honored to proudly work
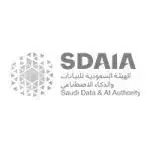
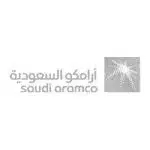
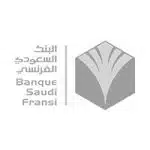
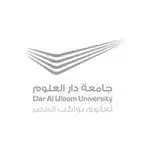
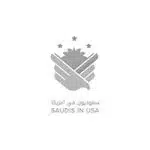
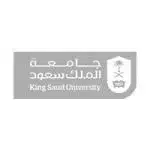
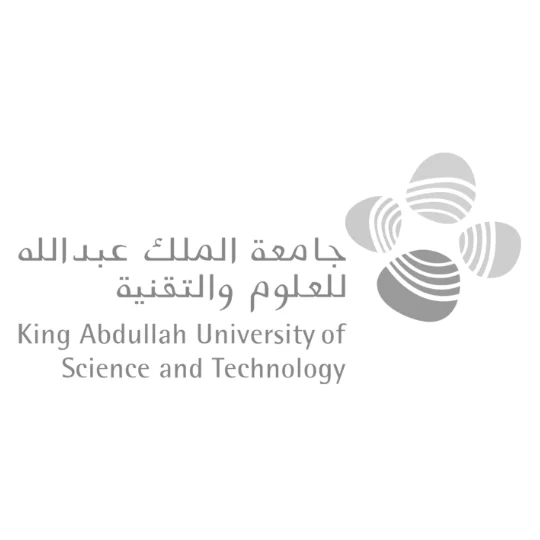
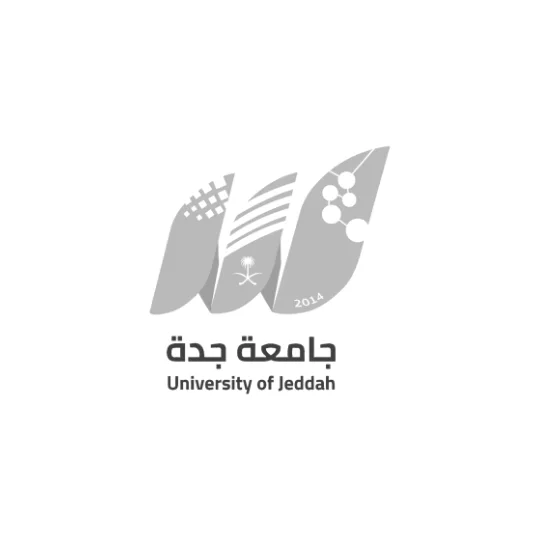
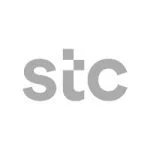
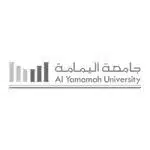
Top training materials
Latest training materials
Our vision
Top-notch technology-driven training content services.
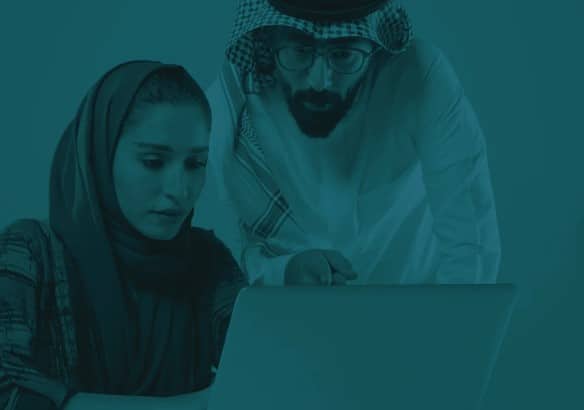
With a rich history of designing training bags, our organization is uniquely and innovatively qualified to bridge the gap between innovation training bags with different luster and permanent development of axes that suit all training updates as well as real solutions required by trainers.
“Our institution offers curriculum-based training modules to enhance organized and effective learning opportunities. The training modules are designed based on predefined frameworks, with a focus on key components to ensure the efficient achievement of your training course objectives. The training package includes interactive learning units and stimulating educational materials, enabling participants to acquire skills comprehensively. ‘Your Toolkit’ aims to provide a customized training experience centered around key components, promoting interaction and a deep understanding of the presented topics.
Hakapetk Foundation provides a unique service in designing and developing interactive electronic training bags dedicated to learning platforms and compliant with SCORM standards. We care about motivating both the trainer and the trainee through an attractive design and effective content. We understand that interactive bags require technical uniqueness, and we guarantee specialized training content in tune with technological innovation. Our services enable an interesting and effective learning experience, seamlessly integrating technology with traditional training processes.
Skills and self-development
Training materials for the development of skills and oneself are fundamental for personal and professional growth. Such materials provide an opportunity to learn new skills and strengthen personal abilities, which contribute to improving performance in the career field and achieving personal goals.
Finance and accounting
Training materials in the fields of Finance and accounting provide professional updates and enhance audit and financial planning skills. Enables participants to effectively understand personal aspects and develop in their professional fields.
Business development
Business Development Training materials offer strategic insights and organizational skills. Contribute to enhancing leadership and innovation capabilities, which enhances organizational success and improves the performance of working teams.
Learn languages
Language learning training materials provide effective and intensive learning experiences. It focuses on developing writing, reading, and speaking skills, helping participants gain a comprehensive and effective familiarity with new languages.
Educational pedagogy
Educational training materials offer innovative teaching strategies and develop classroom organization skills. They contribute to enhancing the effectiveness of teaching and stimulating positive interaction in the learning environment.
Health and sports
Health and sports training materials focus on enhancing fitness and improving lifestyle. It provides specialized training skills and encourages the development of healthy habits and improved athletic performance.
Business applications
Training materials for work applications provide practical skills in the use of advanced technologies and tools. It focuses on developing organizational skills and personal effectiveness to enhance performance in sophisticated work environments.
Technique and technology
Technical and technology training materials offer advanced knowledge and specific technical skills. It focuses on updating participants with the latest technological developments and enhancing their abilities in data analysis and designing innovative solutions.
Get a free consultation now
How can we help you
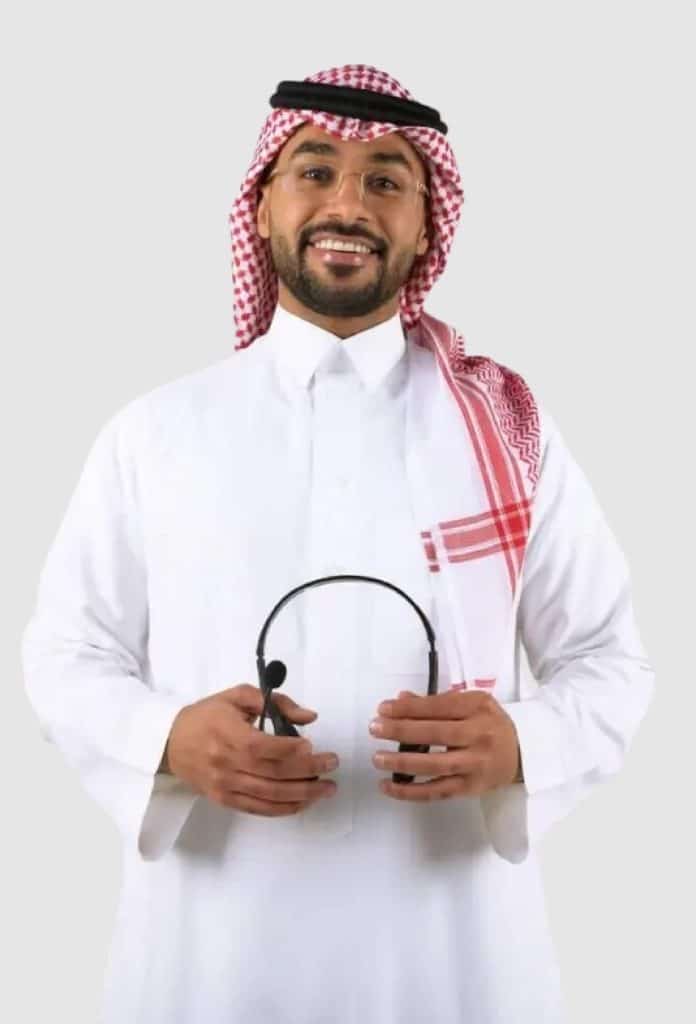
Opinions of our clients
What trainers say about Hakapetk
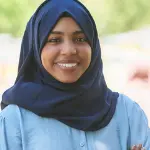
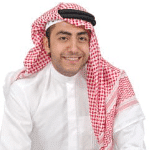

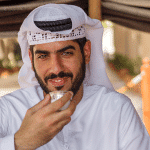
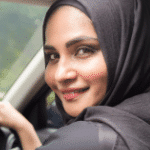
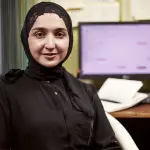
Our goal
We are dedicated to a mission of crafting training content for our MENA.
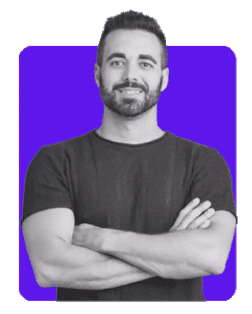
Hamad Al-Rifai
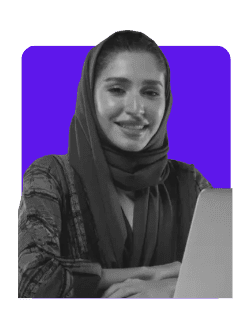
Amal Al-masaoud
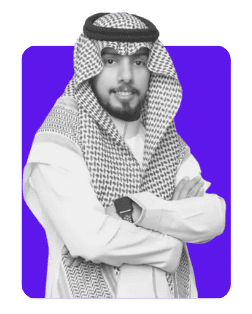
Abdullah Suleiman
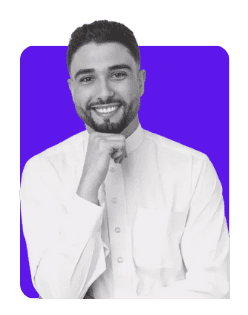
Badr Abdulaziz
Repeatedly
Frequently asked questions
You can get information about the training materials we offer by contacting us via WhatsApp, Where a comprehensive detail is available about the outlines , training content, and skills covered by the training materials. You can also contact the development team by phone 966545301217 for more details.
“Hakapetk” offers comprehensive training materials in all fields, where our development team takes a customized approach to designing each training material according to the needs and requirements of its field. Our dedicated team includes experts in content design and technical innovation, ensuring the delivery of unique and effective learning experiences. We understand the diversity in the fields and strive to meet the training requirements of each sector. Depending on technical knowledge and specialization, we offer customized solutions that promote skill development and excellence in every field.
To meet customer expectations and provide customized training experiences, we can adopt an interactive and participatory approach to software development. This can be achieved by conducting consultation meetings to accurately understand the needs of clients, and analyze the goal of training and target skills. In addition, the content and activities can be adapted to suit the requirements of the selected work team.
We use a variety of training methods that include practical workshops, interactive lessons, and the use of technology to improve learning processes. We make sure to use the latest educational tools to achieve an excellent training experience.
Yes, we can customize the content of the training materials to suit the needs of your team. This allows us to get the most out of training and improve the effectiveness of the learning process.
We have had successful experiences with many companies where they have benefited from our training materials. You can look at the testimonials and recommendations that you find on our website to understand how our materials have positively influenced the performance of previous companies.